Risks and Solutions of Cold box and Cool Block in Equipment Management
- About the cold box
For enterprises engaged in pharmaceutical cold chain logistics related business, the operating costs are mainly concentrated in three modules: infrastructure cost, transportation cost, and equipment cost. As the most widely used cold chain equipment in pharmaceutical cold chain transportation, cold storage boxes, if they can Efficient and reasonable equipment management will save a lot of cost for the enterprise. This article mainly focuses on the risks and solutions in the equipment management of cold storage boxes, hoping to let more practitioners understand, pay attention to, and solve the risks in equipment management, and provide reasonable solutions for reference.
Risk point 1 – the risk of damage caused by the cold box in transit
The logistics industry is a labor-intensive industry. Its level of automation and intelligence is relatively low compared with other industries, and its service level is uneven. Some pharmaceutical cold chain logistics companies cannot form their own capacity networks, and the intermediate links are basically entrusted For external transportation, the cold box will inevitably encounter violent loading and unloading during transportation. When the cold box is stacked at the bottom, it will be squeezed by other heavy objects, or in special cases, it may fall at an oblique angle during transportation. These are all things that we need to consider and solve.
Solution – the risk of damage caused by the cold box in transit
- High-quality carriers get twice the result with half the effort
Choosing a high-quality outsourced logistics carrier may have very good results. It may have a stable, mature, and reliable lower-level carrier for its transportation and guarantee. They have their own understanding and experience for pharmaceutical cold chain logistics.
- Improve the overall quality of cold storage equipments
In view of the risks of cold boxes in transit, the industry’s requirements for the quality of cold boxes are improved, and the existing cold storage boxes are taken to the testing laboratory for objective simulation, and the quantified values of the current cold box’s various aspects of capacity data are obtained, and then according to the actual transportation situation It will be more targeted to improve the quality of the cold box according to the exploration.
Choose a high-quality cold box manufacturer, put forward requirements for materials and manufacturing technology that meet the usage scenarios, and continue to work with the manufacturer during use to further improve the level of the cold box manufacturer, improve the quality of the cold box.
- Strengthen the external protection of the cold box
If the quality improvement of the above-mentioned cold storage box increases too much in process and cost, and the cycle is too long, the overall quality improvement can also be carried out through external protection improvement. By adding non-woven bags, cartons and other materials for outer packaging, the cold storage box as a whole is sent to the testing laboratory for testing or simulation verification to achieve the desired results.
Risk point 2 – the risk of damage caused by improper storage of the cold box
In the process of normal business circulation, cold storage boxes will be temporarily stored in some areas. It may be as short as a few days or as long as a month or two. Improper use will cause different degrees of damage, such as rain immersion, hail and other weather effects, which will have a great impact on the cold box.
Solution – the risk of damage caused by improper storage of the cold box
- Increase return frequency
This is a relatively direct method, but it will lead to an increase in the cost of returning the box and an increase in management costs, and the pressure on our own warehouse will be relatively large, but returning in time can reduce the risk of staying outside. And can speed up the turnover frequency.
- Specify storage location
Find some high-quality storage resources that can be used. If the volume is not large, you can choose some logistics carriers with high-quality storage resources. In this way, we can reduce the risk of leaving the cold box by specifying the storage location.
3, about the cool block
The biggest difference between the cool block and the cold box is that the volume of the cool block is much larger than that of the cold box. If a cold box corresponds to 6 cool blocks, it is 12 cool blocks for one backup and one use. If you want to include different temperature ranges ( 2℃-8℃, 15℃-25℃, 10℃-25℃, etc.) are even more multiplied. For such a large-scale equipment, it is difficult and risky to manage.
Risk point 1 – the risk of loss during the turnover of cool blocks
The cool block is mainly composed of liquids and boxes. With the development of the pharmaceutical cold chain industry, the internal liquids are made of higher quality materials, and the temperature control is more precise and stable, and the cost has also increased several times. In the past, most of the cool blocks were for one-time use, but now the price of high-quality cool blocks has increased, and most of them are reused. This cost cannot be ignored.
In normal business flow, the loss of cool blocks is very common, mainly concentrated in the untimely packing and bringing back after delivery at the end, or unreasonable loss caused by long-term storage in the warehouse.
Solution – the risk of loss during the turnover of cool blocks
- Rigid requirements for logistics carriers to return equipment
Put the equipment return list into the dispatch order, and even the return of the cool blocks can be bound by related expenses. Generally, cold boxes are less likely to be forgotten, and more likely to miss cool blocks. This kind of fine-style restraint will play a certain role.
- Add equipment detail labels to the outer packaging
Add the corresponding equipment list label on the outer packing box, and there are corresponding reminders, for example: 6 pieces of ice rafts are included, please bring them back in time.
Risk point 2 – the risk of cool block leakage
At present, there are basically two types of materials for the ice liquid, one is oily organic solvent, and the other is salty inorganic solvent(inorganic salts). The oily organic solvent are slightly corrosive, while the salty inorganic solvent are relatively heavy, the effect is not as good as organic solvent. Sometimes part of the cool block will leak. Even if the relatively thick HDPE cool block is used, there will still be a risk of liquid leakage to the ice sheet in the event of collisions, drops, etc. during long-term and high-frequency logistics transportation.
Solution – the risk of cool block leakage
- Change the sealing method of the cool block
There are currently several methods of sealing: screw cap, slotted cap, ultrasonic welding cap, and hot-melt sealing. Change the cool block from the original screw-type screw cap and slotted cap to the ultrasonic welding cap and hot-melt seal for sealing, melt the polyethylene at the seal, and then let the seal stick by cooling down. together, so basically there will be no leakage.
- Change the box of the cool block
At present, most of the cool block boxes are made of HDPE polyethylene. One way to reduce the risk of leakage is by increasing the density and thickness of the box. Another way is to fluoride the surface of the ice box, which is equivalent to sealing a protective film on the outside of the box for protection, and it will also effectively reduce the risk of cool block leakage.
- Avoid placing the cool block in a high temperature environment for a long time
Due to the principle of thermal expansion and contraction, if the cool block is placed in a high-temperature environment for a long time, the small pores in the box will become larger due to the high temperature for a long time, which will accelerate the penetration of oil and cause liquid leakage. In daily operation, it is found that there is liquid leakage when the cool block is not damaged, which is generally caused by this situation. As long as the cool block is avoided from being placed in a high temperature environment above 40℃ for a long time, basically there will be little leakage.
Risk point 3——Information management for cool blocks
The number of cool blocks is large, the circulation is fast, and a lot of human participation is required. The large number creates a huge workload, and the fast circulation causes accumulation and extrusion. It will bring great implementation pressure to equipment management.
Solution – Information management for cool blocks
Using RFID technology
Using RFID tags is a good solution. Paste the RFID tags one by one on the cool blocks, and put the cool blocks directly into the cool block pretreatment rack after pasting. All the cool blocks that enter will be automatically identified and uploaded to the system. Similarly, they can be identified in batches when they are out of the warehouse, which will solve the problem of scanning codes one by one.
With the development of science and technology, the degree of automation is increasing day by day. The efficiency of enterprises is not only affected by the technology and skill level of employees, but also depends on the degree of perfection of equipment. Therefore, choosing high-quality and efficient equipment is an important way to improve management.
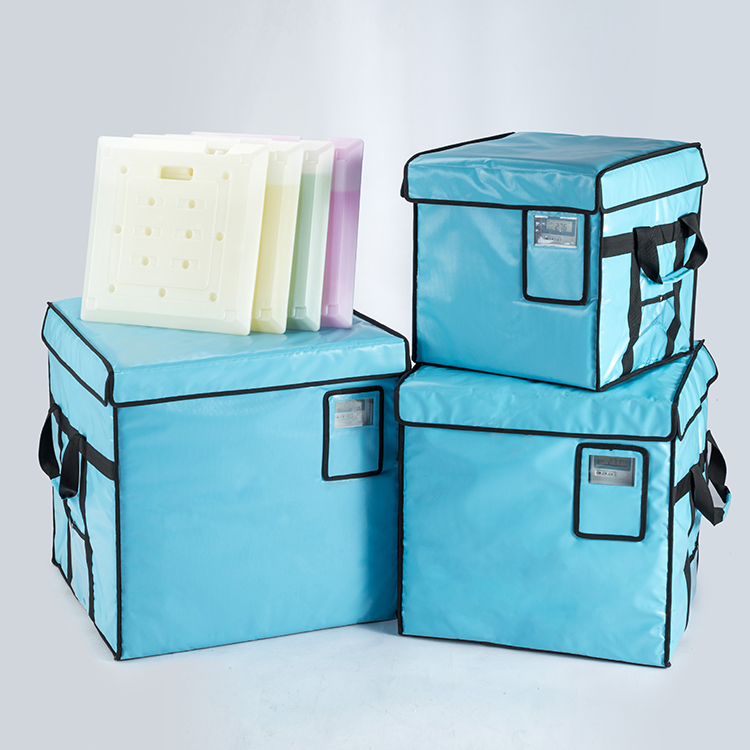
-
Risks and Solutions of Cold box and Cool Block in Equipment Management
-
Which material is good for the cold box, which is both environmentally friendly and practical?
-
Cold chain time- and temperature-controlled transport of vaccines(2)
-
Cold chain time- and temperature-controlled transport of vaccines(1)
-
Various methods of fresh Cold Chain Logistics
-
Vaccine Cold Chain——a hot word
-
The global agricultural product cold chain logistics industry in 2022
-
Three key points of pharmaceutical cold chain logistics
-
Basic knowledge about cold chain transportation of medicines!
-
What is cold chain food?