Cold chain time- and temperature-controlled transport of vaccines(1)
Abstract
Purpose
The objective of this research was to examine the cold chain temperature maintenance for the supply of vaccines and other biological products by pharmaceutical wholesaler.
Materials and Methods
In this study, six configurations using cold vaccine boxes or bags made with different materials, with and without insulation, of different sizes, and number of coolant-packs were used to simulate the configuration used by the pharmaceutical wholesalers for transportation of vaccine. Model vaccines (vial, n=10) were packed using these six configurations which then stored in an incubator at 38℃ and monitored for 24 hours. Each configuration was tested repeatedly for 5 times.
Results
In term of compliance to 2℃–8℃, four out of six tested configurations are effective in cold chain transportation. The effectiveness is highly dependent on the type of passive containers used, size of cold boxes, insulation, and number of coolant-packs. The configuration with a larger polystyrene foam box with five coolant-packs maintained the required temperature up to 23 hours. In contrast, configurations using a polystyrene foam box with four coolant-packs and a large vaccine cold box with two coolant-packs failed to reach below 8℃ throughout the 24 hours.
Conclusion
Packaging method, the material and size of the container could have a direct impact on the effectiveness of cold chain temperature maintenance. Polystyrene foam box, cold box with polyethylene interior lining and polypropylene insulation, a cooler bag with proper number of ice packs could be effectively used for transportation of vaccines within their respective transportation duration allowance.
Keywords:
Cold chain management; Temperature; Pharmaceutical wholesaler; Transportation
Introduction
Vaccines are biological products may loss of potency or even destroyed with each episode of exposure to temperatures below or above the recommended temperature range (2℃–8℃) [1]. To maintain vaccines perfectly conserved right from the manufacturing facility to patient use requires a satisfactory cold chain set-up, compliance to standards, and effective logistic management [2]. The standard procedure of cold chain management should be adhered to the standard consistently whereby the supply chain cycle equipped with rigorous temperature and humidity control throughout the supply chain stages [3]. Improper storage during transportation which may expose vaccines to temperatures outside the recommended ranges can decrease their potency [4].
An accidental event in which a vaccine or other biological product is exposed to temperatures outside the ranges designated for transport and storage is termed as temperature excursion [5]. Temperature excursion refers to keeping vaccines below the recommended temperature which can be as harmful as keeping them above that temperature range, since most vaccines may be damaged by freezing [6]. Therefore, an effective vaccine supply chain and logistics system is crucial to safeguard product quality. One appropriate example is the Thailand case study where a vendor-managed inventory system was used to ensure full compliance of vaccine supply management and distribution [7]. Common pitfalls are non-fully functioning refrigeration apparatus, non-compliance with cold-chain procedures, lack of understanding of the vaccine damage and inadequate monitoring practice [8, 9].
Vaccines, being biological products, have a limited shelf life and the potency of vaccines is guaranteed provided if the stock is transported and stored within the stipulated conditions. The optimum temperature for refrigerated vaccine is between 2℃ to 8℃ whereas for frozen vaccine the minimum temperature is −15℃. Once a vaccine has been thermally compromised, its loss of potency cannot be reversed [1, 2]. Good Distribution and Storage Practices clearly state that temperature-sensitive products should be stored, handled, and distributed with great care throughout the distribution network. This serves as a requirement of temperature monitoring throughout the whole supply chain process [10, 11].
The common necessity of those product storage is the strict high requirements on the temperature, humidity, light, or other particular conditions [1, 2]. For example, since heat and direct sunlight are detrimental to the integrity of vaccine, the storing of vaccine should be in its original packaging until the time of administration. The term “passive container” was used by the World Health Organization (WHO) to describe “a container that maintains a temperature-controlled environment inside an insulated enclosure, generally without thermostatic regulation, using frozen, conditioned, cool, or warm coolant-packs” [2]. Some examples of passive containers used in cold chain are vaccine carriers, reusable insulated cold boxes and single-use insulated cartons [12, 13, 14]. However, there is a gap in the current knowledge and practice on the proper usage of large capacity vaccine cold boxes [14], vaccine cold boxes [13], and carriers [12] because the WHO Performance, Quality and Safety (PQS) catalogue does not list net storage capacity for cold boxes and carriers [12, 13, 14]. According to PQS catalogue, the gross volume can be calculated based on the values for internal dimensions of the vaccine compartment, taking into account of having coolant-packs in place [2]. In this particular case, PQS catalogue only suggests the pharmaceutical wholesaler to load the vaccine carrier or cold box with the designated number of frozen coolant-packs [2].
To the authors’ best knowledge, no study has been reported before to simulate the real performance of cold chain from pharmaceutical wholesaler to their customers such as clinics, hospitals, and pharmacies. Thus, the objective of this study was to evaluate the performance of the packaging methods practised by the pharmaceutical wholesalers, in compliance with the PQS specification stipulated by WHO [2, 12, 13, 14]. This study also served to design a good packaging method for cold chain supply. The study examined various characteristics including the choice of packaging materials, number and arrangement of cold pack as well as duration of transportation.
Materials and Methods
Study design and configurations
There were six configurations of vaccine packaging used for this study (Table 1). For each configuration, a total of 10 vials of anti-tetanus vaccine (Tetanus toxoid vaccine adsorbed; 10 dose vials of 5.0 mL; Serum Institute of India, Pune, India) were. When the vaccines were not in use for experiments, the vials were stored between 2℃ to 8℃ in a refrigerator of which the temperature was closely monitored.
The configuration 1, 2, 4, and 6 simulated the packaging methods used by pharmaceutical wholesalers whereas configuration 3 and 5 were designed to study the impact of different number of coolant-pack(s) used in each packaging. The temperature in each storage configuration was monitored for 24 hours, with each configuration was tested repeatedly for 5 times.
The size of the coolant-pack (Thermafreeze ice pack; Thermarite, Petaling Jaya, Malaysia) was 14.0×6.5 cm and weighted approximately 90.0 g when it was hydrated. Prior to use, the coolant-pack was immersed in water for 15 minutes to be fully hydrated and then placed in the freezer for a minimum of 24 hours to ensure it was fully frozen.
In order to ensure the outer packaging of the vaccine is not soiled and fully dry, the vaccines were protected using a simple and makeshift insulator. The insulator was made up from a low-density polyethylene plastic bag (12.0×16.0 cm) and newspaper. For each configuration, 10 vials with a data logger inserted into a low-density polyethylene plastic bag and opening was tied tightly. Then, the bag was then wrapped with two layers of newspaper.
Time and temperature recording
Each configuration (passive container with vaccine vials and data logger) was left in a large incubator with temperature set at a 38℃ simulating the temperature of transporting vehicle without air-conditioning. Data loggers were used to track the temperature changes inside the package of vaccines, when the vaccines are being sent to the customer. Two temperature and humidity USB data loggers (Alpha TH30; TempSen Electronics, Shanghai, China) which were newly calibrated and validated were used to record internal temperature inside the container and external temperature. The measurement range of the data logger was between −30℃ to 70℃ for temperature and 0%–100% for humidity level. The external data logger which was used to monitor the external temperature for 24 hours to simulate the harsh environment during transportation process. Another data logger that was used to monitor external temperature was placed next to vaccine container to record down the external temperature.
Statistical analysis: comparison of temperature-time profiles
The pair-wise statistical procedure using the difference factor (f1; Equation 1) and f1areawere used to compare the temperature-time profiles obtained. The difference factor measures the percent error between two curves.
(Equation 1) f1={∑nt=1|Rt−Tt|∑nt=1Rt}×100%
[15]
Where Rt and Tt are the cumulative percentage dissolved at each of the selected time points of the reference and test product. When the test and reference profiles are identical, the percent error is zero, and increases proportionately with an increase in dissimilarity between the two temperature-time profiles. Meanwhile, for difference factor f1area, the difference of profiles is calculated based on Equation 2 [16].
(Equation 2) f1area(τ)=∫τ0|WR(t)−WT(t)|dt∫τ0WR(t)dt
Where WR and WT are the reference and test profiles at time t, respectively. Evaluation of f1area was considered up to the time corresponding to time zero to time at 24 hours. In this project f1area was applied from mean data sets. For instance, a f1area=0.20 suggested 20% average difference of a test from a reference data set. For each temperature-time profile comparison, configuration 1 was chosen as the reference profile as configuration 1 is the most commonly practiced method.
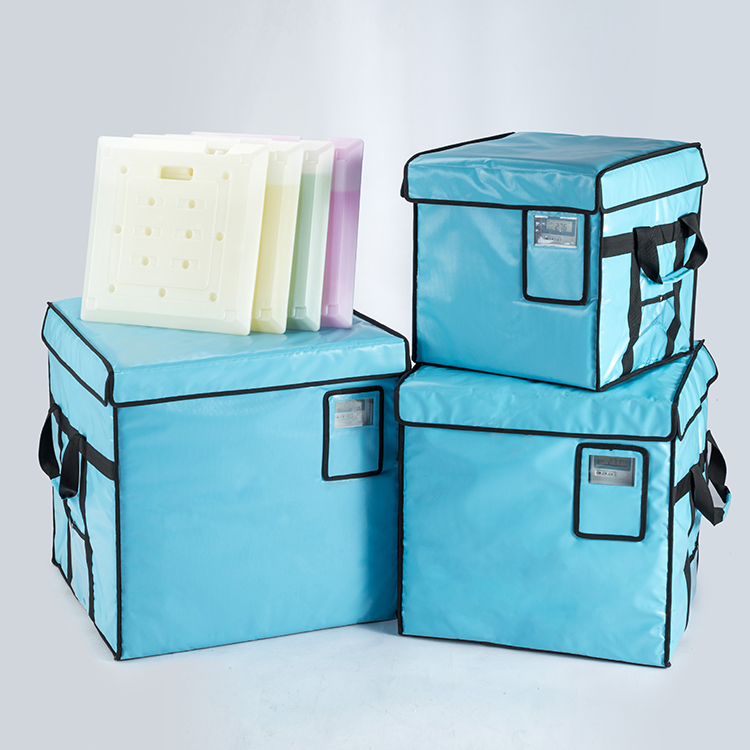
-
Risks and Solutions of Cold box and Cool Block in Equipment Management
-
Which material is good for the cold box, which is both environmentally friendly and practical?
-
Cold chain time- and temperature-controlled transport of vaccines(2)
-
Cold chain time- and temperature-controlled transport of vaccines(1)
-
Various methods of fresh Cold Chain Logistics
-
Vaccine Cold Chain——a hot word
-
The global agricultural product cold chain logistics industry in 2022
-
Three key points of pharmaceutical cold chain logistics
-
Basic knowledge about cold chain transportation of medicines!
-
What is cold chain food?